Noticias
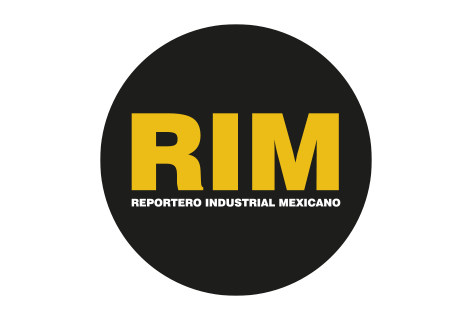
La transformación digital en las máquinas herramienta comenzó ya hace algunos años, no obstante, y como ocurre en prácticamente todos los procesos de manufactura, se ha acelerado recientemente gracias al crecimiento exponencial en la velocidad de procesamiento y del volumen de transmisión de datos.
Las tecnologías de la información están fusionando los mundos digitales con las máquinas herramienta y sus equipos periféricos, llevando información relacionada tanto con los equipos como con los procesos, así como de los productos mismos, lo que facilita también las tareas de administración y mejora de los procesos, tal como sucede con el mantenimiento o el aseguramiento de la calidad.
Podemos decir que la digitalización llega a las máquinas herramienta desde el momento mismo del control numérico, hace más de medio siglo. De hecho, es en 1949 cuando aparece el primer control desarrollado por John T. Parsons en el Instituto Tecnológico de Massachusetts, aunque es en la década de los 70’s cuando comienzan a incorporarse elementos de electrónica y computación moderna, con los que se pudieron ya diseñar —con mayor alcance— algunas trayectorias de maquinado a partir del desplazamiento de herramientas con cálculos y ecuaciones matemáticas.
Desde entonces, y con la estandarización de los sistemas software CAD/CAM, ya en los años 80, la evolución digital de las máquinas herramienta se ha desarrollado notablemente y ha generado mejoras sustanciales en aspectos de eficiencia, precisión y productividad.
Los equipos periféricos, así como los componentes de sujeción y las herramientas de corte, son parte de esta era digital; incorporando sensores y aplicaciones que facilitan el seguimiento de las operaciones, determinan el rendimiento de los procesos de corte o alertan de cambios en las tolerancias establecidas causados por cualquier problema en el maquinado, incluyendo el desgaste de la herramienta.
El arte de la sincronización será el jugador principal en las nuevas propuestas de comunicación en la manufactura, pues un proceso de manufactura es, a su vez, un complejo ensamble de procesos que culminan en la configuración de una articulación productiva. Es por ello por lo que la estandarización de los protocolos de transmisión de datos jugará un rol central en este escenario.
Luego de decir adiós a los restiradores, los equipos de ingeniería y diseño se volcaron hacia las herramientas de software de diseño asistido por computadora (CAD), que pasaron de ser solo trazos bidimensionales a generar diseños tridimensionales basados en tecnologías de objetos y completamente parametrizados, listos para procesos de simulación y de indicaciones para su manufactura, incluyendo las rutas de desbaste a partir de su traslado a herramientas de manufactura asistida por computadora (CAM), cuya interoperabilidad está estipulada en la norma ISO10303-242.
Lea también: Así será la nueva planta industrial basada en la Industria 4.0
La tecnología de información, como enlace de los mundos digitales y físicos, permite mejorar las funcionalidades en los procesos de maquinado tal como la incorporación de cambios de manera segura, sin riesgos para los equipos o en las piezas de trabajo (es decir, sin producir desperdicios), también permite asegurar la recolección de datos relacionadas con el desempeño de la máquina en función con los cambios establecidos, a partir de acciones de simulación.
Esto es posible con modelos de gemelos digitales, cuyo entendimiento y adopción es cada vez mayor, y permite que las operaciones se ejecuten y que se evalúen las operaciones sin que una máquina se eche a andar o sin que una pieza tenga desbaste alguno.
Estos modelos tienen la capacidad de incorporar librerías que además aceleren estas pruebas o ensayos, pues evitan que la generación de los mecanismos o de las piezas se realicen desde cero, incluyendo los parámetros o configuraciones relacionadas con la operación. Los diseñadores, por lo tanto, pueden anticiparse a problemas, los que les permite también eludir gastos relacionados con estas fallas hipotéticas de haberse presentado durante la operación real.
Ya en la operación, el valor de la digitalización sigue incrementándose en el maquinado. Los cerebros de los CNC no solo cumplen con llevar a cabo la ejecución de instrucciones de operación, la cual queda almacenada para su posterior revisión, sino que están cada vez más abiertos a recibir información de otros componentes ajenos a las máquinas en las que están instalados de fábrica.
Por ejemplo, algunos de los nuevos portaherramientas ya incorporan electrónica con la que pueden registrar parámetros clave para determinar el estado de la operación, tales como las revoluciones por minuto (RPM), el registro de los avances reales o la profundidad de ataque; información que es transmitida de forma inalámbrica a un CPU o al mismo CNC. Los operadores podrán ver, en tiempo real, el nivel de vibración, el balanceo de un portaherramientas y otros indicadores que pueden influir de manera directa en el acabado de la pieza de trabajo.
En el caso de las herramientas de corte, se están incorporando softwares que generan códigos basados en los parámetros de corte que ayudan a su vez a asegurar la productividad en la operación y también alargan la vida útil de las herramientas. Adicional a ello, es posible monitorear la producción de virutas que, en si mismas, son un indicador de la calidad de corte.
Son cada vez más las aristas relacionadas con los avances en la digitalización de las máquinas herramienta y que están conformando un ecosistema cada vez más amplio que incluye otras áreas adyacentes, como la metrología que, a partir del estándar QIF, asegura el intercambio de información dimensional de las piezas de trabajo. Todo indica que la metrología incrementará su protagonismo en el proceso, pues si hoy está presente en los portaherramientas de los centros de maquinado, también se incorporará en el seguimiento de la calidad a través de los sensores dispuestos en las herramientas y portaherramientas, sobre todo pensando en tareas de alta producción.
La digitalización permitirá que las empresas metalmecánicas incrementen su competitividad cubriendo desde el diseño, hasta la producción, pasando por la configuración de celdas cada vez más automatizadas ayudadas por componentes que apoyen con el manejo de materiales, como los brazos robóticos bajo esquemas de alimentación (bien conocidos como machine tending).
Todos estos modelos sin duda incrementarán la eficiencia, la calidad, la flexibilidad y reducirán el tiempo ciclo. Los ambientes de máquinas herramienta basados en información están ya transformando a muchas empresas, no solo haciéndolas más productivas, sino permitiéndoles generar nuevas posibilidades en la manera de atacar una operación con rutinas de trabajo mejor coordinadas y con un aspecto más amplio para la obtención de nuevos proyectos.
Otros artículos de interés
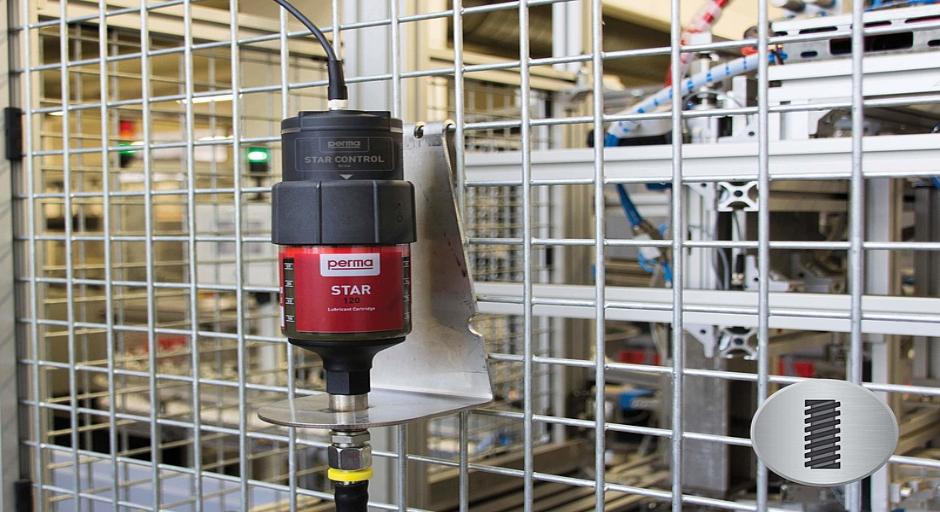
Lubricación automatizada, paso obligado en operación: Perma
En las plantas industriales, la lubricación ha pasado de ser una rutina
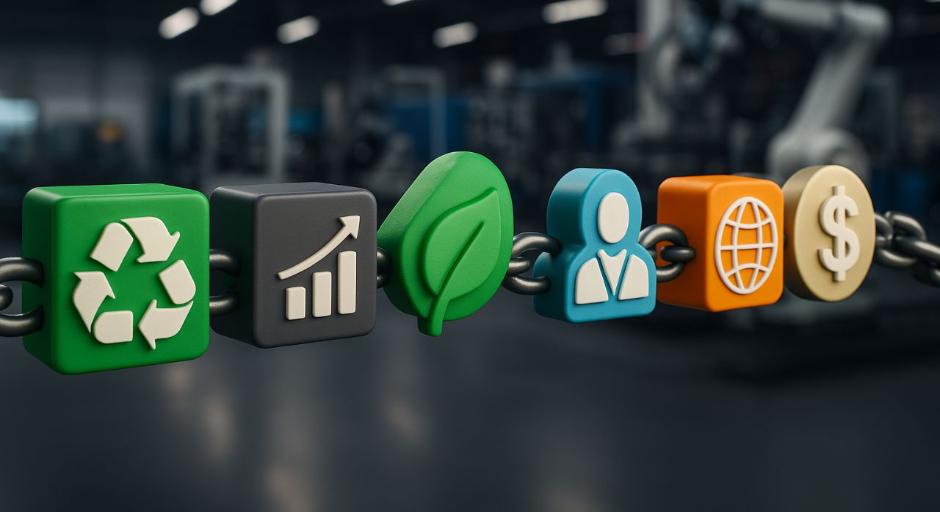
Cuidado ambiental: responsabilidad eslabonada
El cumplimiento de políticas de sostenibilidad en la industria manufacturera se ha
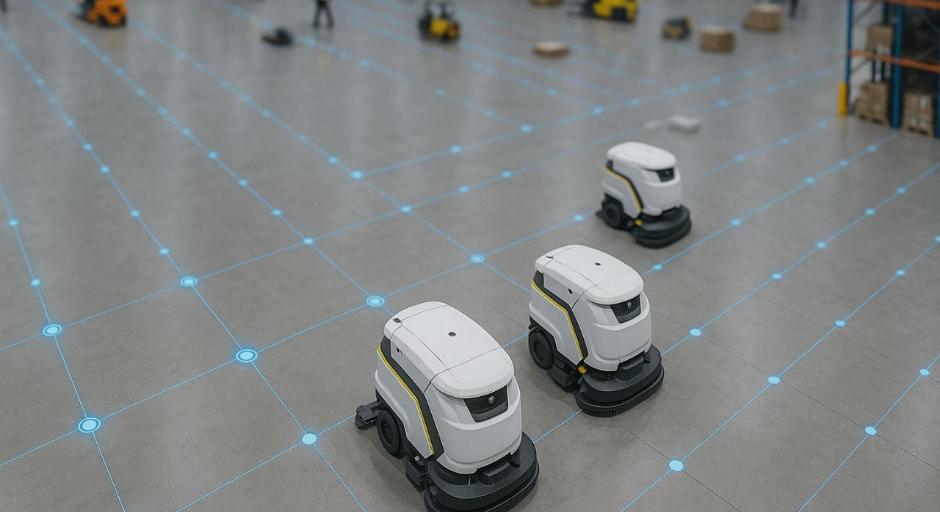
Limpieza industrial no escapa de la automatización
En la industria, la limpieza de áreas productivas es tan importante como

Suministro ininterrumpido para la Industria 4.0
La Industria 4.0 representa un salto evolutivo en la manufactura: sistemas físicos,
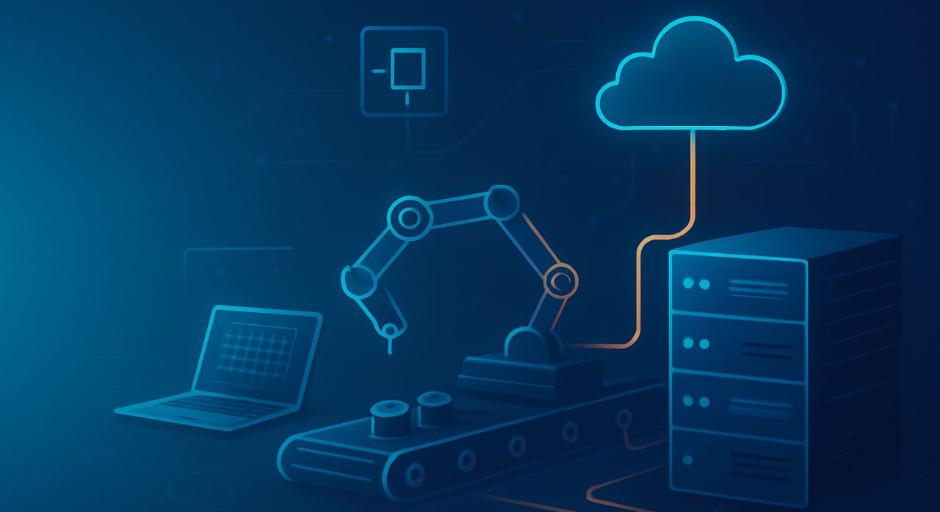
Por qué la manufactura requiere una buena infraestructura de redes
Con la adopción de tecnologías digitales en la manufactura, la infraestructura de

Transporte multimodal gana valor en la industria
En la industria manufacturera mexicana, la logística ha dejado de ser un